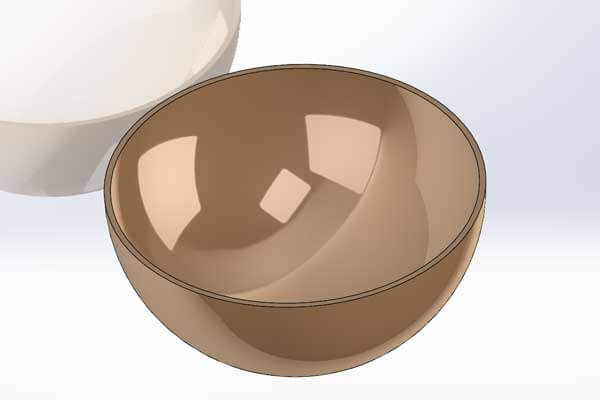
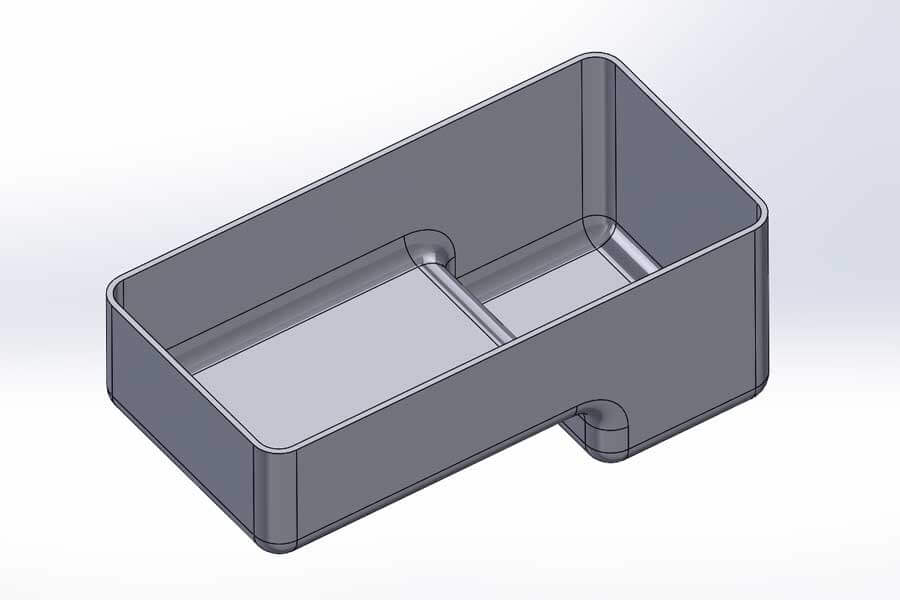
本日は3Dプリントの技術的なワンポイントアドバイスのブログです。
3Dプリントを行っているみなさんなら一度は経験したことがある、接地面積が少ない状態での3Dプリント問題。これは熱溶解積層方式やインクジェット方式、光造形方式などビルドプレート上に造形品がプリントされる形式であれば共通のことです。
写真左の丸いモデルは肉厚が1.5mm、左の四角いモデルは肉厚2mmです。この厚みは成形品としてはごく一般的な厚みですが、平面をビルド面に接地した状態では明らかに接地面積が少なく、3Dプリント中に造形品が脱落してしまう可能性があります。
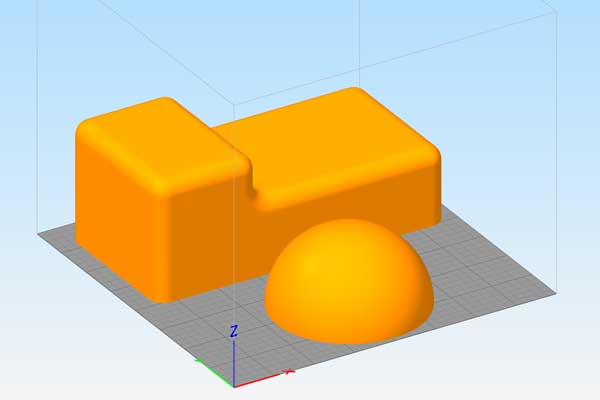
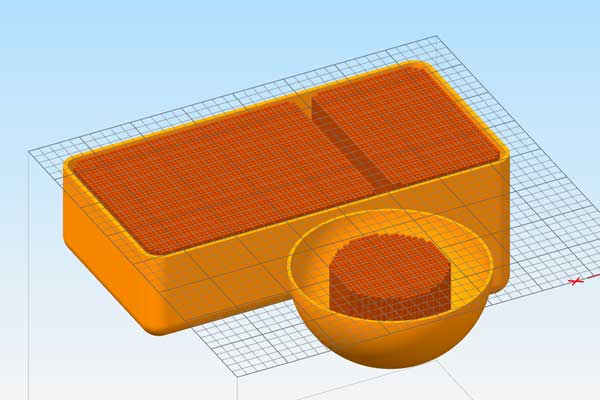
通常はこのように配置して、内部にサポートが立つように配置するかと思いますが、これでは明らかに接地面積が少ないのです。
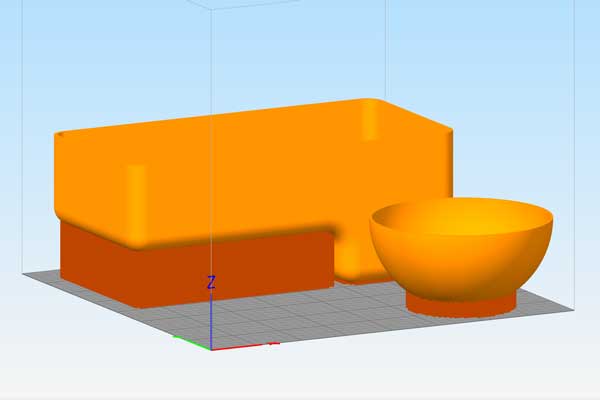
モデルを裏返して配置することもできますが、外観にサポート痕が残ってしまいますし、サポートだけがビルドプレートに接地している状態は、モデル脱落のリスクもあります。
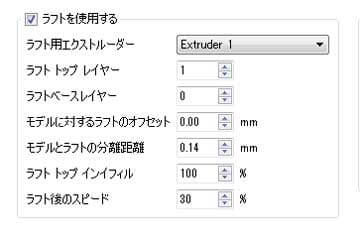
そこでスライサーソフトの中には、ラフトという機能が存在しておりまして、ビルドプレートとモデルの間を一枚の板でつないでくれる機能になります。この機能を使えばモデルとビルドプレート間を強力に接続してくれるため、3Dプリント中の脱落リスクは大幅に減少します。
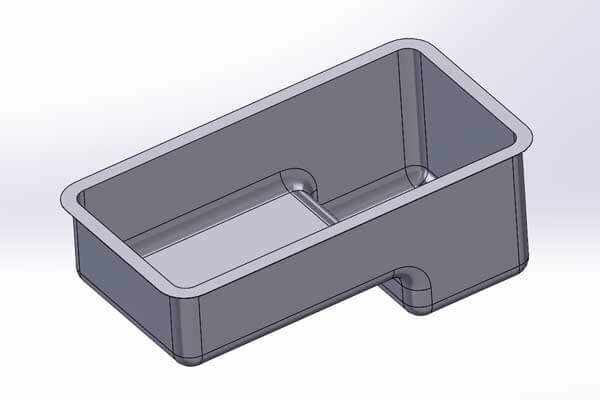
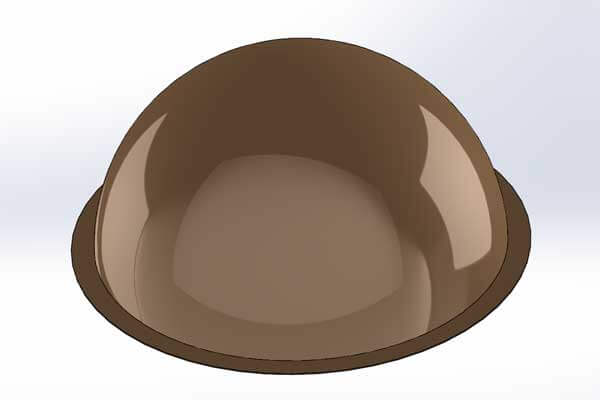
もしスライサーソフトの中にラフト機能がない場合、もしくは設定範囲が狭く、自分の意図したラフトが作れない場合は、3D-CAD上でラフと形状をモデリングすることをオススメします。
例えば熱溶解積層方式で積層ピッチ0.25mmで行っている場合は、0.25mmの厚みのフランジ形状のラフトを底面に作ってあげます。5mm外側に出してあげれば、元の厚みプラス5mmですのでかなりの接地面積になります。そして3Dプリント後は綺麗に手でフランジ部分だけを外すことができます。
このフランジは内側に配置しても問題ありません。外側にする理由は、ビルドプレートからモデルが取り外しやすい(フランジからめくり取ることができる)からです。
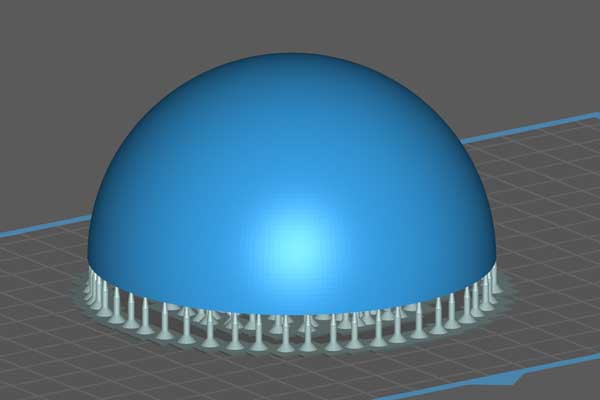
光造形の場合でもこのフランジ形状のラフト方式は使用できまが、(今回の形状では内部の圧力逃しが必要になりますが、詳細解説は割愛)二次硬化後にラフトを外す場合は、本体モデルを破損させないように留意が必要です。
外観的問題がなければ、写真のようにモデル全体を浮かせて、サポートを立てる方が簡単かもしれません。
ビルドプレートに直接造形品が接続されている3Dプリント方式であれば、このフランジ状のラフト作戦は有効でしょう。そして自分でラフトをモデリングすることは最強に汎用性が高いです。自由自在に好きな場所に好きな量のラフトを適宜設定できますので、接地面積の少ない3Dプリントの際にはオススメの技です。是非使ってみてください。