タミヤの塗装ブースの導入
今回はタミヤの塗装ブース用排気マニホールドを3Dプリンターで製作し、既存の排気レジスターを改造して見栄え良く、機能的な塗装ブースを導入する過程をブログにしてみました。右写真の塗装ブースを所有されている方も多いかと思いますが、排気ファンはシングルとツインが選べます。弊社は塗装する量が多いためツインファンタイプを選んだのですが、1つ問題がありまして、2本の排気ホースが独立した状態で1本化するオプションパーツは販売されていないのです。
さすがに1本化しないと外に排気する際に不便ですので、日本のホースを合流させるマニホールドをデザインすることにしました。ネットで検索してみると他の人はY字型の塩ビパイプと接続して合流するなど試行錯誤して1本化しているみたいですが、やはり専用の合流部品があったほうが見た目も良いし、スマートです。
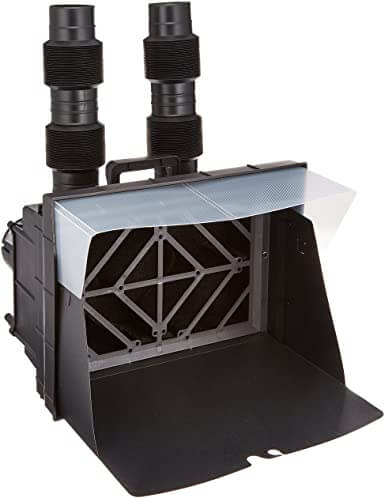
早速モデリング
さっそくホース合流マニホールドをモデリングしてしました。右写真が断面図。下の入口はメス穴になっており、上の出口はオスになって、どちらもタミヤ純正のホースがささるように直径が設定されています。
もちろんABS樹脂で3Dプリントするため収縮も加味して寸法を設定しております。3D-CADなので流体解析を行ってもおもしろかったかもしれませんが、3Dプリンターの造形範囲の限界値の関係で流体効率まで加味してデザインはできませんでした。
裏側には取り付け時に使用するアルミパイプが2本通る穴が横方向に貫通しており、アルミパイプ上でスライドして好きな位置に変更できる仕様になっています。完全ワンオフ製品ですね。
3Dプリントもギリギリ
2本のホース間ピッチは、タミヤ塗装ブースに取り付いた2機のファンのピッチそのままでデザインしたのですが、なんとギリギリ3Dプリンターの造形範囲に収めることができました。奇遇です。熱溶解積層方式3Dプリンターの造形範囲は200×200×170でして、横幅は余裕で造形範囲を超えていたので斜めに入れるしかなかった感じです。ちなみに高さもギリギリでしたので、この3DプリントはMF-1050の中で過去最大の造形物となります。
造形時間はアニール処理も入れて42時間、使用するABS樹脂量は535g、物が大きいので肉厚は3mmに設定しました。射出成形では絶対に作ることができない形状、ブロー成形ででなければできませんが、ブロー成形で作るなら、純正ホース程度の厚みになってしまい、今回のように厚み3mmは製作できません。まさに3Dプリントだからできる形状と言えます。
塗装ブースと合体
早速ファンを起動して流量チェックをしてみましたが、写真の通りティッシュが勢いよく舞い上がり、排気効率も悪くなさそうです。あとは上の出口に純正のホースを取り付けて、換気口へと蛇腹をのばしていけば良いのですが、既存の換気口にそのままホースを差し込むことはできませんので、専用のアダプターもデザインして、既存の開閉機構もそのまま使える仕様にしてみました。
既存の換気レジスターの土台の部分をそのまま使い、開閉機構を使えるようにしました。開閉機構を利用する理由は、冬場の冷気が逆流して室内が寒くならないようにです。後日談ではありますが、開きっぱなしでも真冬の札幌において冷気の逆流は起きませんでしたので、後に開閉機構を抜きにして新たなダクトアダプターを製作しましたが、割愛させて頂きます。
今回マニホールドや排気レジスターアダプターを製作してわかったことは、排気効率が悪くなると、全く排気されないことです。特に排気レジスターの中にはフィルターが入っており、流路が急激にクランクしているのも良くありませんでした。後に製作したダクトアダプターはフィルターレスで流路もストレート形状を採用したため、ファン本来の排気能力を出し効率の良い排気を実現しました。
フィルターレスということで、外壁に塗装粉の付着が心配されますが、数十時間の長期塗装後でも、外壁への汚れは全くありませんでした。フィルターレスとは言え、タミヤの塗装ブース自体にフィルターが付いているため、粉が外に漏れることはほとんどない感じです。
右の写真は3Dプリント中に起きたモジャモジャ現象。かなり久しぶりだったので驚きました。